
Turning Increased Speed at High-Volume Fueling Sites into a Quicker ROI
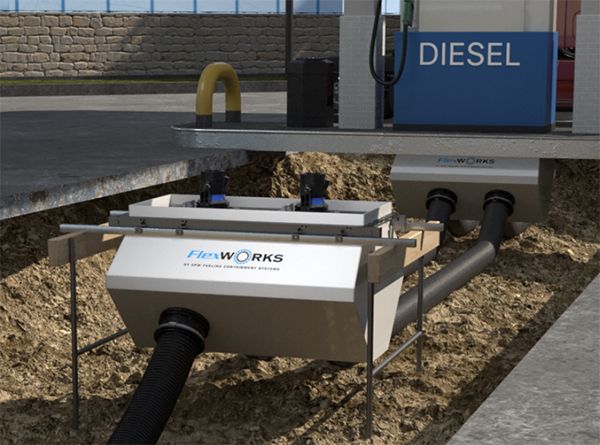
Turning Increased Speed at High-Volume Fueling Sites into a Quicker ROI
By Ed Kammerer
YOU CAN FORGIVE THE DRIVER OF A LONG-HAUL 18-WHEELER IF, AS HE WAITS FOR HIS 120- TO 170-GALLON FUEL TANKS to be refilled at a service station, he channels his inner fighter pilot. You know: “I feel the need, the need for speed.” Unfortunately, other than watching Top Gun for the umpteenth time, that request will likely go unheeded if he is refueling at a truck stop or large hybrid convenience store that has been outfitted with truck lanes, but features a fueling system that caters first and foremost to the refilling rates of automobiles.
Watching from inside the store, the site operator can sympathize in many ways with the driver. When he looks out his window and sees a line of trucks waiting at the fuel island, he’d probably wish that they could be refueled faster, which would increase throughput while lessening the frustration that comes with waiting in line, which, in turn, would lead to higher revenues for his site.
In the end, both the driver and the fueling-site operator have the same goal: optimize their return on investment (ROI). For the driver – whether an owner-operator of his rig or an employee of an over-the-road trucking company – this means spending as little time as possible idled and more of it on the road, which will let him satisfy the strict demands of his delivery schedules, resulting in a better ROI for him and his clients. For the site operator, a fueling site that reliably and efficiently meets the needs of its customers will attract more of them, which will shorten the time needed for the operator to experience a true ROI for his efforts.
The Need For Speed
As mentioned, speed can play a major role in aiding both parties. Specifically, it can do so in three areas:
Installation: A fueling system that can be installed quickly and with little to no need of in-the-field fabrication in the form of drilling, installation of entry fittings, preparing fiberglass joints, connecting, welding and gluing means less downtime and lost revenue for the site operator
Fueling: Trucks that sit at a fueling island for an extended period of time are not on the road making deliveries; getting drivers into and out of the fueling station quicker enables them to do their job more efficiently and cost-effectively, which should be a priority for the station operator
Maintenance: Fueling systems are fine-tuned operational ecosystems that have most of their critical components buried out of sight; identifying a system that allows easy access to underground equipment will make maintenance, inspection, repair and part replacement, if necessary, easier to perform
If the fueling site is able to optimize the speed of installation, fueling and maintenance, the operation will be able to satisfy the basic needs of the operator and the drivers that frequent the site – with an optimized ROI the ultimate reward.
To The Rescue
In 2008, OPW, Smithfield, NC, changed the retail-fueling business with the introduction of the FlexWorks Loop System. The loop system consists of a collection of pre-fabricated underground fueling equipment that needed little, if no, in-the-field construction before it could be installed into the ground, with all post-installation inspections, maintenance, repair and parts replacement able to be performed aboveground.
Specifically, the system offered the following benefits to its users:
All sumps are pre-assembled and tested at the factory, eliminating field fabrication and potential installation errors
All piping connections are accessible through shallow sumps that can be reached from the surface, meaning no concrete needs to be broken, removed and repoured when component repair or replacement is needed
Continuous piping runs eliminate connection points buried in the ground
Double-wall couplers have built-in, permanent test ports for easier monitoring
Piping is installed in access pipe and can be removed, checked and replaced through the sump opening without removing the dispenser or breaking concrete
All told, the loop system was a revolutionary innovation – the fueling industry’s first true plug-and-play fuel-delivery system, one that combined hassle-free component inspection with streamlined installation, maintenance and repair.
Since the introduction of the loop system, the retail fueling landscape has evolved, with a noticeable increase in the number of high-volume fueling sites that are now in operation. Namely, these sites are the large truck stops that can feature 10 to 20 fueling lanes and hybrid c-stores that offer a combination of traditional automobile fueling islands and trucks-only fueling lanes
To meet the needs of these locations, in 2019 OPW launched the HiFlo Loop System, which takes the components of the original variation and supersizes them so they can deliver higher flow rates – all while maintaining the original system’s streamlined installation, operation, monitoring, maintenance, repair and replacement capabilities.
The upgraded components in the new High-Flow Loop System include:
Pre-fabricated loop sumps that accommodate high-speed dispenser footprints, which allow high-volume flow rates while enabling fuel dispensing on both sides of trucks, including a satellite lane
two-inch 10 Plus Shear Valve that matches up with high speed two-inch dispenser inlets while offering all the benefits of the traditional OPW 10 Plus Shear Valve
three x six-inch double-sided hybrid entry fittings (HEF) that provide double containment protection to prevent fuel contamination and groundwater intrusion
three-inch UL971-listed coaxial double-wall pipe that is easy to install, requires no adhesive or welding, and eliminates leak points, exposed joints and fittings buried directly in the ground with no protection
three-inch double-wall, stainless-steel pipe couplings (DPC) that eliminate the need for rubber test boots and the trimming back of secondary jackets, while allowing for continuous monitoring
six-inch access pipe that resists crushing and allows easy access and pipe retraction for maintenance, repair, removal and replacement without ever breaking concrete or the need to remove a dispenser from the island
All of these components are pre-fabricated and pre-assembled at the factory, which makes them ready to be placed in the ground when they arrive at the fueling site. This eliminates the need for labor-intensive drilling, connecting, welding and gluing of the system components, meaning that an installation operation that used to take upwards of two weeks can now typically be completed in one full day – which is the truest definition of optimized speed in applications like these.
Conclusion
Audiences around the world have been thrilled by the exploits of Maverick, Goose and Iceman and their “need for speed” in the 34 years – can it really be that long ago? – since the original Top Gun was released. With the introduction of the HiFlo Loop System from OPW Retail Fueling, high-volume fuel-site operators and the long-haul drivers who patronize their sites are now able to fill a similar speed need at the fueling island, with a quicker ROI the desired payoff.
Ed Kammerer is the director of global product management for OPW, based in Cincinnati, OH, USA. He can be reached at ed.kammerer@opwglobal.com For more information on OPW, go to OPWGlobal.com