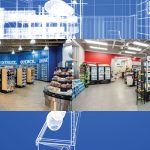
A Look at Fiberglass-Manufacturing Methods and Their Applications

By Ed Kammerer
In many ways, human beings are driven by the search for the next big thing, something that’s “new and improved” or “bigger and better.” As an example, take smartphones. As soon as the newest model is released, the people who stood in line to purchase it immediately begin wondering when the next model will become available. In reality, there are many, many people whose lives are moving along just fine with a smartphone model that was released several years earlier.
Which brings us to fiberglass. The first patent for fiberglass – defined as a “type of fiber-reinforced plastic using glass fibers” – was awarded in 1880, with the fiberglass that we recognize today entering the market in the mid-1930s. Since then, it has become an indispensible component in the production of many common objects, including bathtubs, swimming pools, roofing and boats.
It also has a prominent place in the forecourt of your local retail-fueling station. Fiberglass is commonly used in many of the components (seen and unseen) that dot the forecourt, including manhole covers, dispenser and tank sumps, top hats and skirts. And much like that smartphone, the ways to construct and implement fiberglass have evolved and expanded over the years. At this point, there are four main methods – all of which are viable and commonly used – to manufacture fiberglass-based forecourt products.
A Totally Full Glass
The trick, then, for the fueling-site operator is choosing forecourt components and equipment that make the best use of the specific fiberglass-manufacturing processes. Let’s take a closer look at each one, from oldest to the most recent innovation:
- Open-Mold Spray Up: Also known as “chop and spray,” this method uses a specialized gun outfitted with a bottle of resin to apply a pre-mixed, spooled fiberglass strand to a single-sided mold. In addition to its low cost, the main benefit of this method is that it is easier to produce parts that are of an irregular shape (not circular or square), as well as parts that are not meant to have an airtight or watertight seal or bear heavy loads and forces. The main drawback is that a part can only be produced with one smooth side and the thickness can be less consistent than those produced by other methods, since the fiberglass/resin is sprayed on by hand. It can also lead to an inconsistent blend of resin and glass fibers leaving porous or weak spots in the product. Hand rollers are used to squeeze out any air pockets, but if any air pockets are missed, this will also compromise the consistency and quality of the finished product.
- Resin-Transfer Molding (RTM): Uses a composite of glass fibers and resin that is packed into a mold, with the fiberglass providing tensile strength and the resin contributing compressive strength to the finished product. To ensure a smooth, consistent finish on both sides of the object, all of the fiberglass fibers must be fully saturated with the resin. This is accomplished by layering glass sheets into a mold and then injecting the mold with resin. The two components are then compressed together by extreme forces in a hydraulic press that insures a perfect blend of resin-saturated glass. This method of construction is effective in developing dense, compact layers of fiberglass for objects that need to bear heavy loads or repeated high-force events, such as manhole covers. The drawbacks to this method come in the actual manufacturing process itself, which requires expensive tooling and a large hydraulic press to ensure that the two halves of the mold hold together effectively.
- Vacuum-Assisted Resin Transfer Molding (Vac-RTM): This evolutionary stage in the RTM method uses a vacuum to pull, rather than push, the resin into the fiberglass. This creates a better seal without the need of a large, expensive hydraulic press, with something as simple as a pair of vice-grip pliers used to securely clamp the two halves together. The finished walls are also incredibly smooth, which makes it easier to attach things to it, while there are no holes or pores that can adversely affect sealing capabilities. The biggest challenge with this method is the simple fact that there is an absolute maximum amount of force that can be generated by a vacuum. This limits the amount of fiberglass that can be permeated by the resin, which restricts the load-bearing properties of the finished product and, by extension, the number of different products it can be used in. This process makes it ideal for parts like containment chambers, but not manhole covers.
- Sheet-Molded Compound (SMC): This most recent fiberglass-manufacturing innovation combines the best of the chop-and-spray and RTM methods. It’s basis is a putty-type mixture of resin and chopped glass fibers that is produced in sheets that can then be molded to meet the specific end-user needs for density, length, and shape. The sheets are cut to the size and shape needed, then placed in a mold and pressed into shape. The result is a part that has the highest level of consistency available, making it the premier way to construct a high number of consistent parts over a short period of time. The main drawback goes back to the heart of the manufacturing process – a large (sometimes 20-foot tall) and expensive hydraulic press is needed to shape the fiberglass sheets into a finished product. The other drawback is the high initial tooling cost and capital expense. The mold that is placed into the press is a large, precision-machined piece of steel that is made into the exact shape of the part to be pressed. The tool is then chrome-plated for easy release from the press. The SMC process is ideal for high-volume parts requiring consistent and detailed end results.
OPW Retail Fueling, Smithfield, NC, utilizes all four types of fiberglass-manufacturing processes in creating its various lines of manholes, dispenser and tank sumps, multiports, top hats and skirts. Its latest effort in this area is the new DSE Series Dispenser Sump, which combines best-in-class quality, fast lead times and affordability without the customer having to accept less than the best level of performance in all three metrics.
The DSE dispenser sumps are constructed via the SMC manufacturing method, which gives them extremely fast lead times, smooth walls both inside and outside, which allows entry fittings to bond better and prevent leaks, and a consistent finish and thickness that can accept all types of piping and fittings. Finally, the DSE sumps are stackable, which optimizes distributor inventory space and improves ease of ordering.
Conclusion
While we love bigger and better, sometimes same-old, same-old can still be the best solution. Though the ways to manufacture fiberglass have grown over the years, all four common methods still have their advantages when it comes to building components for use in the retail-fueling forecourt. The task is finding parts that make the best use of the specific manufacturing method, from top hats and skirts that are still made through the chop-and-spray method, to next-generation dispenser sumps like the OPW DSE Series that take advantage of the advanced SMC process.
Ed Kammerer is the director of Global Product Management for OPW, based in Cincinnati, OH, USA. He can be reached at ed.kammerer@opwglobal.com. For more information on OPW, go to www.OPWGlobal.com.